When drinking water comes from the sea
The benefits of seawater desalination are obvious: seawater is a crisis-proof and practically inexhaustible resource, available in sufficient quantities at all times, regardless of precipitation, surface water and groundwater. In addition, drinking water obtained from seawater is of excellent quality.
Until recently, the high costs of desalinated water, which are mainly due to the high energy demand, worked against its use. However, technological innovations are making the plants more economical, so demand is currently on the rise.
Trending: reverse osmosis
In the past, thermal plants, where seawater is evaporated by heating in a multi-stage process, played the most significant role, but today the more energy-efficient reverse osmosis plants are increasingly gaining acceptance.
In reverse osmosis (abbreviated as RO), the seawater is pressed through membrane filters under high pressure. The fine-pored filters are designed so that the water molecules are forced through the membranes while salts and minerals are retained.
To protect the membranes from damage, the seawater must be carefully treated in advance and thoroughly cleaned of foreign bodies, suspended particles and other impurities. This is usually done by macro-filtration in, for instance, sand filter basins, followed by micro-filtration. After reverse osmosis the filtrate undergoes re-mineralisation, in which minerals are re-introduced before the treated water can be delivered into the drinking water supply.
The energy requirement for reverse osmosis is significantly lower than for thermal processes. The high-pressure pumps in the RO unit, which generate the pressure required for reverse osmosis, are responsible for a large part of the energy consumption. By recovering the pressure energy contained in the remaining concentrate, the already lower energy requirement can be further reduced. There are also further improvements in membranes which reduce operating costs. These and other factors mean that seawater desalination is becoming more economical and more important for the supply of drinking water.

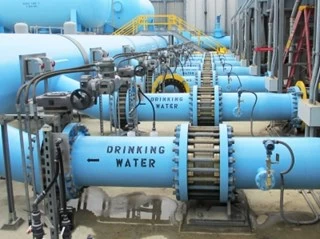
Carlsbad
desalination plant
The Carlsbad Desalination Plant is currently the largest reverse osmosis plant in
the Western hemisphere. The plant near San Diego, California, which is
exemplary in terms of environmental protection and energy efficiency, has been
in operation since 2016 and delivers approximately 200,000 cubic metres of
high-quality drinking water each day.
Approximately 500 AUMA electric actuators are used in this modern plant.
Electric actuation technology was given preference in Carlsbad because of its
simple installation, high reliability in virtually maintenance-free operation,
and low operating costs. The robust SA actuators for open-close duty and SAR
for modulating duty are mainly used in conjunction with the powerful GS
part-turn gearboxes and the intelligent AC controls. The actuators are
integrated into the control system over Profibus DP, contributing to the
consistently high degree of automation in the flagship plant.
The actuators operate a wide variety of gate, butterfly and ball valves in all
process steps, from seawater extraction, via sand filtration, micro-filtration,
RO unit and remineralisation, to feeding into the drinking water network. In
the cleaning processes that are periodically required, they automate the supply
of rinsing and cleaning solutions and rinsing air as well as the recycling of
residual materials.
Highest corrosion
protection
Salt is omnipresent in Carlsbad. The actuators are constantly exposed to the
salty sea air blowing over from the Pacific. The media in the pipelines are
also aggressive – not just the seawater, but also and in particular the
concentrated brine which is a by-product of reverse osmosis. These media are
not just a challenge for pipelines and valves, which are usually made of
special corrosion-resistant materials. Potential leaks may also cause actuators
to come into direct contact with seawater or highly corrosive brine.
Excellent corrosion resistance is essential to withstand the saline atmosphere
and the aggressive media. Here, the AUMA actuators prove their worth with their
corrosion protection, certified by TüV Rheinland. Even the standard version
meets the requirements of the highest C5-M corrosion category for highly saline
atmospheres and almost constant condensation in accordance with ISO 12944-6.
This high corrosion resistance is due to the extremely robust two-layer AUMA
powder coating. Each housing part is individually coated before assembly. This
means, for example, that housing covers can be dismantled during installation
without any problems: in contrast to wet painting a fully assembled device, the
powder coating – and thus the corrosion protection – remains intact. Another
special feature is the powder coating ‘behind the sealing edge’, which includes
the flange surfaces and groove for the sealing ring wherever the aggressive
atmosphere can penetrate. This also prevents corrosion on the flange faces.
Under high
pressure
The high pressure at which the seawater is forced through the membranes also
places high demands on the actuators. For example, strong vibrations often
occur in the vicinity of the high-performance pumps. Here, the modular AUMA
actuators offer the benefit that the actuator controls with electronics can be
mounted separately from the actuator, at distances up to 100 metres. Since
there is a risk of pressure surges due to the high pressure in the pipeline,
bypass lines are installed in the seawater supply system at Carlsbad. The AC
actuator controls contain an interlock function that ensures that the main
valve is only closed if the valve in the bypass is fully open.
For fine adjustment of flow rate and pressure, AUMA SAR modulating actuators
are used, for example, on the high-pressure pumps upstream of the RO unit and
on the feed pumps for the treated drinking water, each combined with a GS
part-turn gearbox. These actuators are specially designed for frequent operation
and high positioning accuracy, and meet the requirements for Class C modulating
duty according to EN 15714-2. In the GS part-turn gearbox, a bronze worm gear
provides the high wear resistance required for modulating duty.
Conclusion
In Carlsbad as well as in numerous other desalination plants all over the
world, AUMA electric actuators demonstrate that they meet the high demands
placed on them. In particular, the TüV-certified high corrosion protection
guarantees lasting, reliable valve automation. The modular product design with
actuators, gearboxes and integral controls enables comprehensive single-source
solutions for all seawater desalination tasks. In addition, a worldwide sales
and service network in over 70 countries offers fast and skilled local support.