The instruction of pneumatic actuators
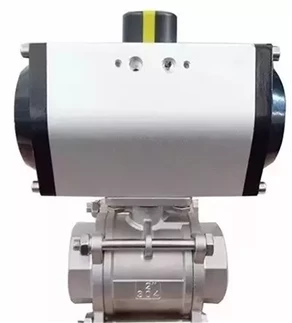
First. Overview of pneumatic actuators
Pneumatic actuators are actuators that use air pressure to drive opening and closing or control valve valves. They are also called pneumatic actuators or pneumatic devices, but they are generally called pneumatic actuator. The actuator and adjustment mechanism of the pneumatic actuator are a unified whole, and the actuator has a membrane type, a piston type, a fork type and a rack and pinion type.
The piston type has a long stroke and is suitable for occasions requiring greater thrust; while the membrane type has a small stroke and can only directly drive the valve stem. The fork-type pneumatic actuator has the characteristics of large torque, small space, and the torque curve is more in line with the torque curve of the valve, but it is not very beautiful; it is commonly used on valves with large torque. The rack-and-pinion pneumatic actuator has the advantages of simple structure, stable and reliable action, and safety and explosion protection. It is widely used in the production process with high safety requirements such as power plants, chemical industries, and oil refining.
Second, the working principle of pneumatic actuator
1. Working principle diagram of double-acting pneumatic actuator
When the air source pressure enters the cavity between the two pistons of the cylinder from the air port (2), the two pistons are separated and moved toward the ends of the cylinder. The air in the air chambers at both ends is discharged through the air port (4), and the two piston racks are synchronized at the same time Drive the output shaft (gear) to rotate counterclockwise. Conversely, when the air source pressure enters the air chambers at both ends of the cylinder from the air port (4), the two pistons move toward the middle of the cylinder. The air in the middle air chamber is discharged through the air port (2), and the two piston racks simultaneously drive the output shaft (gear) ) Rotate clockwise. (If the piston is installed in the opposite direction, the output shaft will become reverse rotation)
High pressure floating ball valve can be installed with this type pneumatic actuator
2. Working principle diagram of single-acting pneumatic actuator
When the air source pressure enters the cavity between the two pistons of the cylinder from the air port (2), the two pistons are separated and moved toward the ends of the cylinder, forcing the springs at both ends to compress, and the air in the air chambers at both ends is discharged through the air port (4). Synchronize the two piston racks to drive the output shaft (gear) to rotate counterclockwise. After the air source pressure is reversed by the solenoid valve, the two pistons of the cylinder move in the middle direction under the elastic force of the spring, the air in the middle cavity is discharged from the air port (2), and the two piston racks simultaneously drive the output shaft (gear) Rotate clockwise. (If the piston is installed in the opposite direction, the output shaft will turn into reverse rotation when the spring is reset).
Third, the classification of pneumatic actuators
1. Membrane actuator
Diaphragm actuators are the most commonly used. They can be used as a driving device for general control valves to form a pneumatic diaphragm actuator. The signal pressure p of the pneumatic diaphragm actuator acts on the diaphragm to deform it, and drives the push rod on the diaphragm to move, so that the valve core is displaced, thereby changing the valve opening. It has simple structure, low price, convenient maintenance and wide application.
Pneumatic membrane actuators have two forms of direct action and reverse action.
When the signal pressure from the controller or valve positioner increases, the downward movement of the valve stem is called a positive acting actuator; when the signal pressure increases, the upward movement of the valve stem is called a counteracting actuator. The signal pressure of the positive acting actuator is passed into the membrane air chamber above the corrugated diaphragm; the signal pressure of the counteracting actuator is passed into the membrane air chamber below the corrugated diaphragm. By replacing individual parts, the two can be retrofitted to each other.
2. Piston type actuator
The pneumatic piston actuator makes the piston move in the cylinder to generate thrust. Obviously, the output force of the piston type is much greater than that of the film type. Therefore, the membrane type is suitable for occasions with small output and high precision; the piston type is suitable for occasions with large output, such as large diameter, high pressure drop control or butterfly valve pushing device. In addition to the membrane type and the piston type, there is also a long-stroke actuator, which has a long stroke and a large torque, which is suitable for outputting angular displacement and high torque.
The signal standard received by the pneumatic actuator is 0.02 to 0.1MPa.
The main components of the pneumatic piston actuator are the cylinder, piston and push rod. The piston in the cylinder moves with the pressure difference between the two sides of the cylinder. According to the characteristics, it is divided into two types: proportional type and two-position type. According to the two-position type, the piston is pushed from the high pressure side to the low pressure side according to the operating pressure on both sides of the input piston. The proportional type is to add a valve positioner on the basis of the two-position type, so that the displacement of the push rod is proportional to the signal pressure.
3. Rack and pinion actuator
The rack-and-pinion type (double-piston rack type) pneumatic actuator has the characteristics of compact structure, beautiful appearance, quick response, stable operation and long service life. All accessories adopt the most advanced anti-corrosion treatment technology, which can adapt to various harsh working conditions. Its high and low temperature and various special stroke actuators have good performance in various application fields.
Fourth, the selection of pneumatic actuators
Before selecting a pneumatic actuator, please confirm the valve torque. And increase the safety value in the torque, water vapor or non-lubricating liquid medium increases the safety value by 25%; non-lubricating slurry liquid medium increases the safety value by 30%. For high pressure ball valve such as 1500LB F316L ball valve torque should be calculated very carefully when we selecting actuator.
When the valve torque is 210NM, the air source pressure is only 5bar, and the medium is non-lubricated water vapor, taking into account safety factors, increase the safety value by 25%, which is 262NM. Find the corresponding torque when the air source pressure is 5bar according to the double-acting output torque table. value. Should choose 277NM, the model is POADA300.
▼Pneumatic actuator torque table
Five, the performance characteristics of pneumatic actuators
1. The rated output force or torque of the pneumatic device should meet the requirements of GB/T12222 and GB/T12223. The above is a membrane type actuator;
2. Under no-load conditions, input the specified air pressure into the cylinder, and its action should be stable without jamming and creeping phenomena;
3. Under the air pressure of 0.6MPa, the output torque or thrust of the pneumatic device in the opening and closing directions should not be less than the value indicated on the pneumatic device label, and the action should be flexible, and no permanent deformation and Other abnormal phenomena;
4. When the maximum working pressure is used for the sealing test, the amount of air leaking from the respective back pressure side is not allowed to exceed (3+0.15D) cm3/min (standard state); leaking from the end cover and output shaft The air volume is not allowed to exceed (3+0.15d) cm3/min;
5. The strength test is performed with 1.5 times the maximum working pressure. After the test pressure is maintained for 3 minutes, no leakage and structural deformation are allowed in the end cover and static seal of the cylinder;
6. The number of operating life, the pneumatic device simulates the action of the pneumatic valve, and the number of opening and closing operations should not be less than 50,000 (one opening-closing cycle is one) while maintaining the output torque or thrust capacity in both directions;
7. Pneumatic device with buffer mechanism, when the piston moves to the stroke end position, no impact is allowed.