Valve seal introduction
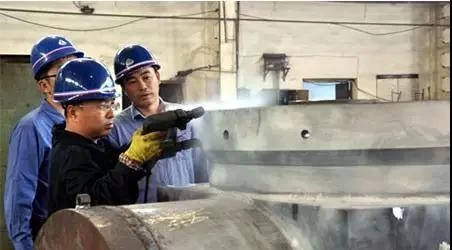
The requirements for valve sealing performance should be based on the prevention of leakage. According to the different parts and degrees of its leakage, the leakage of the valve is different, so different leak prevention measures need to be proposed. As a China Hastelloy C276 high pressure seal gate valve supplier Cowinns gives some introduction as below:
1 valve sealing principle
Sealing is to prevent leakage, so the principle of valve tightness is also studied from leakage prevention. There are two main causes of leakage. One is the most important factor affecting the sealing performance, that is, there is a gap between the sealing pairs, and the other is the pressure difference between the two sides of the sealing pair. The principle of valve tightness is also analyzed from four aspects: liquid tightness, gas tightness, leakage channel sealing principle and valve sealing pair.
11Liquid tightness
The liquid tightness is determined by the viscosity and surface tension of the liquid. When the leaking capillary of the valve is filled with gas, the surface tension may repel the liquid or introduce the liquid into the capillary. This creates a tangent angle. When the tangent angle is less than 90 °, the liquid will be injected into the capillary, which will cause leakage. Leaks occur because of the different nature of the media. Experiments with different media will give different results under the same conditions. It may be water, air gas, or the like kerosene. Leakage also occurs when the tangent angle is greater than 90 °. Because it is related to the oil or wax film on the metal surface. Once the film on these surfaces is dissolved, the characteristics of the metal surface change, and the liquid that was originally repelled will invade the surface and leak. In view of the above, according to Poisson's formula, the purpose of preventing leakage or reducing the amount of leakage can be achieved when the capillary diameter and medium viscosity are large.
2 Gas tightness
According to Poisson's formula, the gas tightness is related to the gas molecules and the viscosity of the gas. Leakage is inversely proportional to the length of the capillary and the viscosity of the gas, and is proportional to the diameter of the capillary and the driving force. When the diameter of the capillary is the same as the average degree of freedom of the gas molecules, the gas molecules will flow into the capillary with free thermal motion. Therefore, when we are doing the valve sealing test, the medium must use water to play the role of sealing, and air or gas cannot play the role of sealing. Even if we reduce the capillary diameter below the gas molecules through plastic deformation, we still cannot stop the gas flow. The reason is that the gas can still diffuse through the metal walls. So when we do gas tests, we must be stricter than liquid tests.
3 sealing principle of leakage channel
The valve seal is composed of two parts consisting of unevenness spread on the wave surface and waviness of the distance between the peaks. Under the condition that the elastic strain force of most metal materials in China is low, if the sealed state is to be achieved, it is necessary to raise the compressive force of the metal material, that is, the compressive force of the material exceeds its elasticity. Therefore, when designing the valve, the sealing pair is matched with a certain hardness difference to match, and under the action of pressure, a certain degree of plastic deformation sealing effect will be produced. If the sealing surface is made of metallic materials, uneven bumps will appear at the earliest. At first, a small load can be used to plastically deform these uneven bumps. When the contact surface increases, the unevenness of the surface will become plastic-elastic deformation. At this time, the roughness of the two sides in the recess will exist. When a load that can cause severe plastic deformation of the underlying material is applied, and the two surfaces are in close contact, these remaining paths can be made close together along the continuous line and the hoop direction.
4 valve sealing pair
The valve sealing pair is the part where the valve seat and the closing member close when they contact each other. The metal sealing surface is susceptible to damage from sandwiched media, media corrosion, abrasive particles, cavitation and erosion during use. For example wear particles. If the wear particles are smaller than the surface unevenness, the surface accuracy will be improved without deterioration when the sealing surface is running in. On the contrary, it will deteriorate the surface accuracy. Therefore, in the selection of wear particles, we must comprehensively consider the material, working conditions, lubricity and corrosion of the sealing surface and other factors. Like wear particles, when we choose a seal, we must comprehensively consider various factors that affect its performance in order to play a role in preventing leakage. Therefore, those materials that are resistant to corrosion, abrasion and erosion must be selected. Otherwise, the lack of any one of the requirements will greatly reduce its sealing performance.
2 main factors affecting valve sealing
There are many factors affecting valve sealing, mainly the following:
1 Sealed substructure
Under the change of temperature or sealing force, the structure of the sealing pair will change. And this change will affect and change the mutual force of the sealing pair, thereby reducing the performance of the valve seal. Therefore, when choosing a seal, be sure to choose a seal with elastic deformation. At the same time, pay attention to the width of the sealing surface. The reason is that the contact surfaces of the sealing pair cannot completely match. When the width of the sealing surface increases, the force required for the seal must be increased.
2 Specific pressure of sealing surface
The specific pressure of the sealing surface affects the sealing performance of the valve and the service life of the valve. Therefore, the specific pressure of the sealing surface is also a very important factor. Under the same conditions, too high specific pressure will cause damage to the valve, but too low specific pressure will cause the valve to leak. Therefore, we need to fully consider the appropriateness of the specific pressure when designing.
3 Physical properties of the medium
The physical properties of the medium also affect the sealing performance of the valve. These physical properties include temperature, viscosity, and surface hydrophilicity. The temperature change not only affects the relaxation of the seal pair and the change of the size of the part, but also has an inseparable relationship with the viscosity of the gas. Gas viscosity increases or decreases with increasing or decreasing temperature. Therefore, in order to reduce the effect of temperature on the sealing performance of the valve, when designing the sealing pair, we must design it as a valve with thermal compensation such as an elastic valve seat. Viscosity is related to the permeability of the fluid. When under the same conditions, the greater the viscosity, the less the fluid's permeability. Surface hydrophilicity means that when there is a thin film on the metal surface, this thin film must be removed. Because this thin layer of oil film will destroy the hydrophilicity of the surface and cause the passage of fluids to be blocked.
4 Quality of sealing pair
The quality of the sealing pair mainly means that we have to check the selection, matching and manufacturing accuracy of materials. For example, the valve disc fits the sealing surface of the valve seat well, which can improve the sealing performance. The characteristic of many annular corrugations is its good labyrinth sealing performance.
Valve leakage is very common in life and production. It will cause waste or harm to life. For example, the leakage of tap valve will cause serious consequences, such as toxic, harmful, flammable, explosive and chemical industry. Corrosive leakage, etc., seriously threaten personal safety, property safety and environmental pollution accidents. A valve that is opened and closed by external force rotation transmission is designed with a sealing device. It is used to fill a certain number of packing seals in the packing culvert to achieve the sealing effect, but what about the sealing situation? The leakage at the packing of the valve is one of the most prone to leak failures in the valve, but there are two main reasons for this.
3 valve seal form
Seals are also critical components in valves. The sealing performance of a valve refers to the ability of each sealing part of the valve to prevent medium leakage, and it is the most important technical performance index of the valve.
There are three places where the valve is sealed:
The contact between the opening and closing member and the two sealing surfaces of the valve seat; the joint between the packing and the valve stem and the stuffing box; the connection between the valve body and the valve cover. The previous leak is called internal leakage, which is commonly known as improper closing, which will affect the valve's ability to intercept the medium. For shut-off valves, internal leakage is not allowed. The latter two leaks are called external leaks, that is, the medium leaks from the inside of the valve to the outside of the valve.
Leakage can cause material loss, pollute the environment, and cause accidents in severe cases. For flammable, explosive, toxic or radioactive media, leakage is not allowed, so the valve must have reliable sealing performance.
How to solve the sealing problem is not a trivial matter, the valve is running, running, dripping, leaking, and so on. Next, we will discuss the dynamic and static sealing of the valve.
1 Dynamic seal
The valve is dynamically sealed and the main finger is sealed. Preventing the medium in the valve from leaking with the movement of the valve stem is the central issue of valve dynamic sealing.
1) Form of stuffing box
The valve is dynamically sealed, mainly with stuffing boxes. The basic form of stuffing box is:
(1) Gland type
This is the most used form.
The unified form can be distinguished in many details. For example, in terms of compression bolts, T-bolts (for low-pressure valves with a pressure of ≤16 kg / cm2), stud bolts and articulated bolts can be divided. From the gland, it can be divided into integral type and combined type.
(2) Tightening nut type
This type has a small external size, but its pressing force is limited, and it is only used for small valves.
2) filler
Inside the stuffing box, the packing is in direct contact with the valve stem and filled with stuffing box to prevent the medium from leaking. The following requirements are imposed on the filler:
(1) Good tightness;
(2) erosion resistance;
(3) the friction coefficient is small;
(4) Comply with medium temperature and pressure.
Frequently used fillers are:
(1) Asbestos packing: Asbestos packing has good resistance to temperature, erosion and corrosion, but when it is used, the sealing effect is less secure, and it is always impregnated or additional materials. Oil-soaked asbestos packing: There are two basic structural forms, one is twisted and the other is braided. Divided into circles and squares.
(2) Teflon braided packing: Teflon braid is woven into packing, which has excellent corrosion resistance and can be used in cryogenic medium.
(3) Rubber O-ring: Excellent sealing effect under low pressure. The use temperature is limited, such as natural rubber can only be used at 60 ° C.
(4) Plastic molding filler: Generally made into three pieces, but also can be made into other shapes. The plastic used is mostly polytetrafluoroethylene.
In addition, for example, in a 250 ° C steam valve, asbestos packing and lead rings are alternately superimposed, the leakage of steam will be reduced; there are valves, and the medium is often changed. , The sealing effect is better. To reduce friction on the valve stem, there are places where you can add molybdenum disulfide (M0S2) or other lubricants.
New fillers are being demanded. Teflon-impregnated with an emulsion, for example, polyacrylonitrile fibers, and after pre-oxidation, sintering mold pressure system, excellent sealing performance can forming filler; and if the filler is made of stainless steel sheet and waveform asbestos, high temperature, High pressure and erosion.
3) Bellows seal
The chemical industry and the atomic energy industry have grown rapidly, and flammable, explosive, highly toxic, and radioactive materials have increased. There are more stringent requirements for valve sealing. There are no places to use packing seals, and a new type of seal-a bellows seal. This type of seal does not require packing and is also called unfilled seal.
Both ends of the bellows are welded to other parts. When the valve stem is raised and lowered, the bellows expands and contracts, the bellows does not leak by itself, and the medium cannot leak out. For safety reasons, double seals with bellows and packing are often used.
2 Static seal
What is a static seal?
Static seal usually refers to the seal between two stationary faces. The main sealing method is to use gaskets.
1) Gasket material
(1) Non-metal materials: such as paper, linen, cowhide, asbestos products, plastics, rubber, etc.
Paper, hemp, kraft, etc., have pores and are easy to penetrate. They must be impregnated with oil, wax or other impervious materials when used. Valves are rarely used in general.
Asbestos products, asbestos tape, rope, board and asbestos rubber board. The asbestos rubber sheet has a dense structure, good pressure resistance, and good temperature resistance. The valve itself and the valve are adjacent to the pipe flange, which is extremely common.
Plastic products have good erosion resistance and are widely used. Varieties include polyethylene, polypropylene, soft polyvinyl chloride, poly tetrafluoroethylene, nylon 66, and nylon 1010.
Rubber products are soft in quality. All types of rubber have certain resistance to acid, alkali, oil, and seawater. Varieties include natural rubber, styrene-butadiene rubber, nitrile rubber, neoprene, isobutyl rubber, polyurethane rubber, fluorine rubber and so on.
(2) Metal materials: Generally speaking, metal materials have high strength and strong temperature resistance. But lead is actually not like this, just take its resistance to dilute sulfuric acid. Frequently used varieties are brass, copper, aluminum, low carbon steel, stainless steel, monel, silver, nickel and so on.
(3) Composite materials: for example, metal-clad (internal asbestos) washers, combined wave washers, and entangled washers.
2) Regular use of gasket properties
When using a valve, it is often the case that the original gasket is replaced. Frequently used washers are: rubber flat washers, rubber O-rings, plastic flat washers, Teflon-coated washers, asbestos rubber washers, metal flat washers, metal profiled washers, metal-coated washers, wave washers, and entangled washers.
(1) Flat rubber washer: easy to deform and not difficult when pressed, but with poor pressure and temperature resistance, it is only used for low pressure and low temperature. Natural rubber has certain resistance to acids and alkalis, and the use temperature should not exceed 60 ° C. Neoprene can also resist certain acids and bases, use temperature 80 ° C. Nitrile rubber is resistant to oil, can be used up to 80 ° C. The temperature performance is also stronger than ordinary rubber, and it can be used in the medium of 150 ℃.
(2) Rubber O-shaped gasket: the shape of the cross section is a perfect circle, which has a certain self-tightening effect. The sealing effect is better than the flat gasket, and the pressing force is smaller.
(3) Plastic flat washer: The most characteristic of plastic is that it has good corrosion resistance, and the temperature resistance of plastic is not good. Polytetrafluoroethylene is the crown of plastics, with excellent corrosion resistance and wide temperature resistance, and can be used for a long time in the range of -180 ° C to + 200 ° C.
(4) PTFE gasket package: full play to the advantages of PTFE, it is less flexible at the same time to make up for shortcomings, made of polytetrafluoroethylene wrapped rubber rubber rubber gaskets or asbestos. In this way, it has the same corrosion resistance as the Teflon flat gasket, but also has excellent elasticity, which enhances the sealing effect and reduces the pressing force.
(5) Asbestos rubber gasket: cut from asbestos rubber sheet. Its components are 60 to 80% asbestos and 10 to 20% rubber, and fillers, vulcanizing agents, etc. It has good heat resistance, cold resistance, chemical stability, abundant supplies and cheap prices. When in use, the pressing force is not necessary. It can adhere to metals, and it is best to apply a layer of graphite powder to avoid laborious disassembly.
(6) Metal hot coil: lead, temperature resistance 100 ℃; aluminum 430 ℃; copper 315 ℃; low carbon steel 550 ℃; silver 650 ℃; nickel 810 ℃; Monel (nickel copper) alloy 810 ℃, stainless steel 870 ℃ . Among them, lead has a poor pressure resistance, aluminum can withstand 64 kg / cm2, and other materials can withstand high pressure.
(7) Metal anisotropic washer:
Lens gasket: self-tightening, used in high pressure valves.
Oval washer: also belongs to high pressure self-tightening washer.
Conical double gasket: used for self-care sealing under high pressure.
In addition, there are square, diamond, triangle, tooth, dovetail, B, C, etc., generally only used in high and medium pressure valves.
(8) Metal-coated gasket: Metal has both excellent temperature and pressure resistance and excellent elasticity. Foreskin materials include aluminum, copper, low-carbon steel, stainless steel, and Monel alloy. It is filled with asbestos, polytetrafluoroethylene and glass fiber.
(9) Wave washer: It has the characteristics of small pressing force and good sealing effect. Often used in the form of a combination of metal and non-metal.
(10) Entangling entangled washer: It is a thin metal band and non-metallic band that are closely attached together, entangled into a multilayer circle, the cross section is sea wave-shaped, has good elasticity and tightness. The metal strip can be constructed with 08 steel, 0Cr13, 1Cr13, 2Cr13, 1Cr18Ni9Ti, copper, aluminum, titanium, Monel alloy and so on. Non-metallic belt materials include asbestos, polytetrafluoroethylene, etc.
In the above, some figures have been listed when describing the performance of the gasket. It must be noted that these numbers have a close relationship with the flange form, medium conditions, and installation and repair technology. They can be crossed, not reached, and the pressure and temperature resistance properties are also converted to each other. For example, the temperature is high, the pressure resistance is often reduced These subtle issues can only be appreciated in practice.
4 valve sealing material
The valve sealing material is an important part of the valve seal, and it serves as the direct contact surface of the valve seal. What are the valve sealing materials? We know that there are two types of valve sealing ring materials: metal and non-metal.
The valve sealing material is an important part of the valve seal, and it serves as the direct contact surface of the valve seal. What are the valve sealing materials? We know that there are two types of valve sealing ring materials: metal and non-metal. The following is a brief introduction to the conditions of use of various types of sealing materials, and commonly used valve types
1 synthetic rubber
Synthetic rubber is better than natural rubber in comprehensive properties such as oil resistance, temperature resistance and corrosion resistance. Generally, the operating temperature of synthetic rubber is t≤150 ℃, and the natural rubber is t≤60 ℃. Rubber is used for the sealing of stop valves, gate valves, diaphragm valves, butterfly valves, check valves, pinch valves and other valves with nominal pressure PN≤1MPa.
2 nylon
Nylon has the characteristics of small friction coefficient and good corrosion resistance. Nylon is mostly used for ball valves and globe valves with a temperature t≤90 ℃ and a nominal pressure PN≤32MPa.
3 Teflon
Polytetrafluoroethylene is mostly used for globe valves, gate valves, ball valves, etc. at a temperature t≤232 ° C and a nominal pressure PN≤6.4MPa.
4 cast iron
Cast iron is used for gate valves, globe valves, plug valves, etc. for temperatures t≤100 ° C, nominal pressure PN≤1.6MPa, gas and oil.
5 Babbitt
Babbitt alloy is used for ammonia stop valve with temperature t-70 ~ 150 ℃ and nominal pressure PN≤2.5MPa.
6Copper alloy
Common materials for copper alloys include 6-6-3 tin bronze and 58-2-2 manganese brass. Copper alloy has good abrasion resistance. It is suitable for water and steam with temperature t≤200 ℃ and nominal pressure PN≤1.6MPa. It is often used in gate valves, globe valves, check valves, plug valves, etc.
7 Chrome stainless steel
The commonly used grades of chrome stainless steel are 2Cr13 and 3Cr13, which have undergone quenching and tempering treatment and have good corrosion resistance. It is often used for valves with water, steam, petroleum and other media with temperature t≤450 ℃ and nominal pressure PN≤32MPa.
8 Chrome nickel titanium stainless steel
The commonly used grade of CrNiTi stainless steel is 1Cr18Ni9ti, which has good corrosion resistance, erosion resistance and heat resistance. It is suitable for steam, nitric acid and other media with temperature t≤600 ℃ and nominal pressure PN≤6.4MPa, and is used for globe valve, ball valve, etc.
9 Nitriding steel
The commonly used grade of nitriding steel is 38CrMoAlA. After carburizing, it has good corrosion resistance and scratch resistance. Commonly used for power station gate valve with temperature t≤540 ℃ and nominal pressure PN≤10MPa.
10 Boronizing
The boronizing process is to directly process the sealing surface from the valve body or disc body material, and then perform boronizing surface treatment. The sealing surface has good abrasion resistance. Used in power plant drain valve.
Besides seal materials ,As a China Hastelloy C276 high pressure seal gate valve manufacturer,Cowinns also design the high pressure seal structure for gate valves. It can perform a good seal function for high pressure and high temperature mediums.